Lean MSP: What do the 8 Wastes Look Like in an MSP?
BY IT GLUE | June 08, 2017
Last week, we introduced you to the concept of the Lean MSP, and talked a bit about the 8 Wastes of Lean in a general sense. If you’re serious about cutting waste in your MSP, you need to be familiar with all of them. By understanding the areas where lean philosophy can have the most impact, your team to get some quick wins and start to think lean. This is critical – lean is part philosophy, part system and part organizational culture. You have to believe in it at a core level. Learn all the Japanese terms, adopt the philosophy, and come to hold a deep-rooted loathing for waste in all its forms.
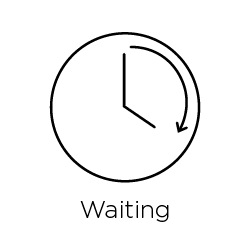
Muda #1 – Waiting
The first waste is waiting. For MSPs, this is a big one. It’s the gap between when a client calls with a problem and the time the ticket is resolved. Think about this wasteful process. A ticket comes in, and your Tier 1 grabs it. But the Tier 1 needs some information and doesn’t know where to find it. Turns out you’re the only one who has the answer. It doesn’t matter how long it takes the tech to get the answer from you – all of that time is wasted time. And while that time is wasting, the tech isn’t doing anything productive, and the client isn’t getting what they want, either.
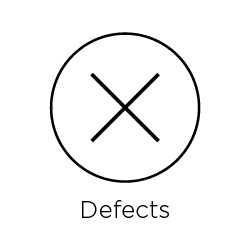
Muda #2 – Defects
The second waste is defects. When your information is disorganized, there are going to be times when you don’t have all of the information you need because you can’t find it. Or worse yet, it doesn’t exist at all. So either the work is delayed (time waste) or somebody takes a shortcut and you get errors. A lean MSP is focused on time to resolution, and structures its operations around making it easier for its techs to resolve issues quickly – and with 100% client satisfaction.
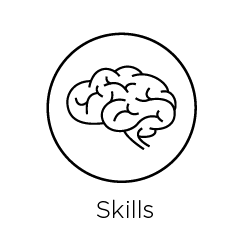
Muda #3 – Skills
The third waste is skills. This is where you have hired talented people, but it takes a long time to get them up to speed. Not just onboarding, but the time to get a Tier I producing at a Tier III level can be years. Shorten that time and get more out of the skills of each tech you have, faster. Don’t waste talent, develop it. Talent working below its potential is wasted, and in many cases not long for your company, which is even worse.
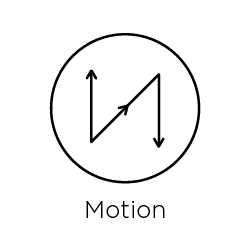
Muda #4 – Motion
The fourth waste is motion. In manufacturing this speaks to economy of physical motion. Obviously at an MSP there are few incremental gains from having a tech’s fingers flow across the keyboard at 100 wpm, so what does motion mean in the MSP context? Well, it reflects how many clicks to get what you want. How many steps to solve a problem. Finding ways to make mental processes efficient is the service industry equivalent of physical processes at a manufacturing firm.
The Other Mudas
The other wastes may be less important, but there are some good opportunities to learn from them as well. Transportation is a form of waste – think about how long it takes information to move in your system…like the pace at which you onboard a new client. Inventory matters – things like simplifying your stack, and ensuring that everything is perfectly documented.
Overproduction and overprocessing – make sure your team is focused simply on the task at hand, solving the client’s issue. This might even be more applicable to MSP sales and marketing, where a lot of surplus energy can be lost if you’re not careful, barking up all the wrong trees.
The “Why?”
Understanding what the sources of waste are is important, because it provides you with tangible areas to target. Remember that lean is a data-driven approach, so start thinking about what processes offer the most promise for improvement and start measuring them. That way, you’ll be able to measure the effectiveness of the changes you make to reduce waste. More on the process by which lean can help MSPs to eliminate waste in our post next week.
To learn more about how IT Glue can contribute to waste reduction, check out our demo.
The IT Glue platform is aimed at eliminating time waste, by ensuring that the information you need has been documented, and is available at your fingertips when you need it. Since 2013, we have been helping IT service providers to reduce organizational waste, and enjoy virtually instant ROI. By leveraging lean philosophy, an MSP can optimize its revenue, minimize its costs, and deliver superior customer satisfaction.